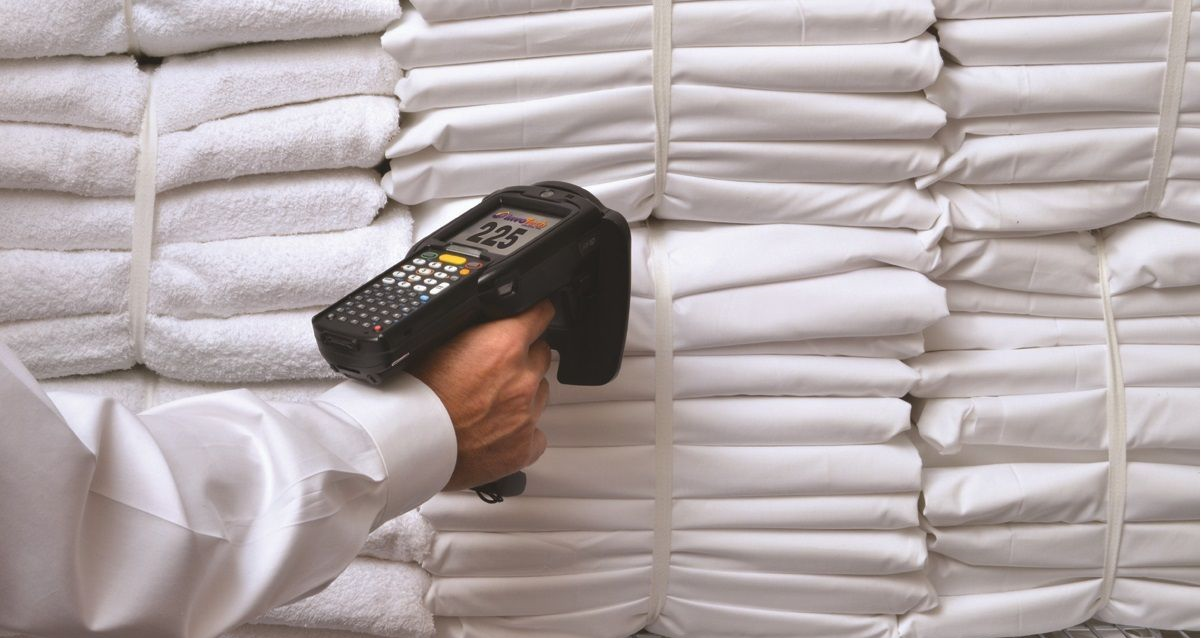
By Harvey Welles, CEO of InvoTech Systems.
Many laundries are turning to UHF-RFID technology to gain better control of their operations and reduce costs. Early installations prove the technology works. UHF-RFID tracking systems save time and money by instantly and accurately identifying and tracking vast numbers of items. These systems process laundry articles infinitely faster and 99 percent more accurately than any other method.
Laundries report the following results from UHF-RFID tracking system use:
* Fewer losses and lower inventory replacement costs
* Total control identifies loss points and enables remedial actions
* Improved labor productivity
* Automated, instant data entry without hand counts, manual tabulations or reporting
* Fewer customer complaints
* Validated deliveries and pick-ups at customer locations
* Improved revenue opportunities and long-term customer relations
* Tag and track customer-owned goods or rental items
These advantages have not been achieved without some setbacks and lessons learned. Here are three tips for making the right UHF-RFID selection for your operation.
Choose the Correct Tag
Tags are a major component of the total cost for the UHF-RFID laundry project. While waterproof UHF-RFID laundry tags from major providers meet international performance standards, they are not created equal. Tags differ in terms of size and appearance, application method, and durability. These differences may impact a laundry operator’s project benefits. Consider the following before choosing the UHF-RFID tag to use:
* Not all tags withstand severe laundry processes, such as sterilization and high pressure water extractors. Ask for performance specs.
* Sewing tags into the seams of items may be best, especially if done by the manufacturers. Tag size is critical if you plan to do this. Discuss tag size with your
manufacturers.
* Larger, heat-sealable tags work well for industrial uniforms, standard linens, etc., but will not work for terrycloth items and are less appealing for high-end items and exacting clients.
* Some tags can be directly sewn onto items. But this does not work well for all items.
* If pouches are used to attach the tags, smaller tags are preferred.
* If customer-owned items are being tagged, make sure you have approval.
Using a combination of two different tags is often the correct choice. It may be necessary to use multiple tag providers or choose a provider that can source both types of tags.
UHF-RFID Equipment Selection and Setup
High quality readers and antennas that meet or exceed international standards at very reasonable prices are readily available. Price, performance, durability and client service should always be considered. But your choice is not wholly about price and technology. It is essential that you also match equipment to your operating environment. Here are 4 tips to make a better UHF-RFID system decision:
* Are you processing large batches or small lots? The size and shape of the article read area influences the type and quantity of antennas you will need. Evaluate your facility with an experienced provider.
* Is the same function always tracked at a particular location – e.g., stain removal, pre-wash, rag-out, etc? Such stations may not require computers.
* Are you processing uniforms or linens? Table-top antennas and portable handheld readers work well with uniforms. Linens require a laundry cart reading station.
* Do you require immediate feedback and confirmation of transactions across multiple locations? Verify that your prospective RFID system supplier has multi-facility capability. In this case, processing speed, high speed network, and Internet compatibility become important.
These are just the initial questions you need to answer to make an informed system selection that will be as cost effective and labor-efficient as possible. The antenna array layouts are very important. UHF-RFID read areas must be properly established to avoid missed or erroneously read tags. The best equipment with a poor setup will yield poor results.
The Importance of Reliable Software and Easy to Use Reports
Selecting the right Software is essential to effectively analyze and apply the data generated by the tracking hardware. Well-designed laundry tracking software will greatly improve labor efficiency. There are UHF-RFID Laundry Systems available that can be configured to meet the needs of various laundry operations. A company may also develop its own custom software.
Here are essential qualities of well-designed, easy to use UHF-RFID laundry management software:
* User-Interface – Software should be easy and intuitive to use. As many functions as possible should be automated to maximize labor productivity and minimize human error. Multi-language capability is a plus.
* Scalability and Growth – The software should be able to grow as your business grows. New features and capabilities should be readily available as your operational needs change.
* Software Support and Maintenance – You will need it; so make sure your vendor provides quality service and support, including software updates.
* Link to Your Customers – A key benefit of your UHF-RFID laundry tracking system is improved customer relations. Your tracking software should directly inform your customers about the status of their orders. Also, more and more customers have their own internal linen and/or uniform tracking systems. Your laundry software should be able to interface directly with those systems. Ask prospective suppliers about this.
* Validate Shipments at the plant and at customer sites – This is another key element to improve customer service as well as eliminating losses during transit.
* Link to Laundry Accounting System – RFID tracking software cannot replace your accounting system but should update it automatically.
Good decisions are based on experience. We can all learn from the missteps and successes of others. You will find you gain control, improve operations, increase revenue and profitability with a well designed and implemented UHF-RFID laundry management system.
About the Author
Harvey Welles is CEO of InvoTech Systems. Welles founded InvoTech in 1991. Today it is a leading provider of software management and control systems for uniforms and linens, laundry and security operations. Under Welles, InvoTech introduced ultra-high frequency (UHF) RFID tag tracking solutions that track laundry and garments in bulk much more efficiently than manual processes. Welles was instrumental in establishing a corporate culture dedicated to state-of-the art service coupled with time-honored courtesy. With his son Jeff, as InvoTech’s president, Harvey describes his role as orchestra leader and conductor. “Leadership is a matter of setting an example and following through on it every day. One has only to look at the projects InvoTech’s team accomplishes to know it is a formula that works.”