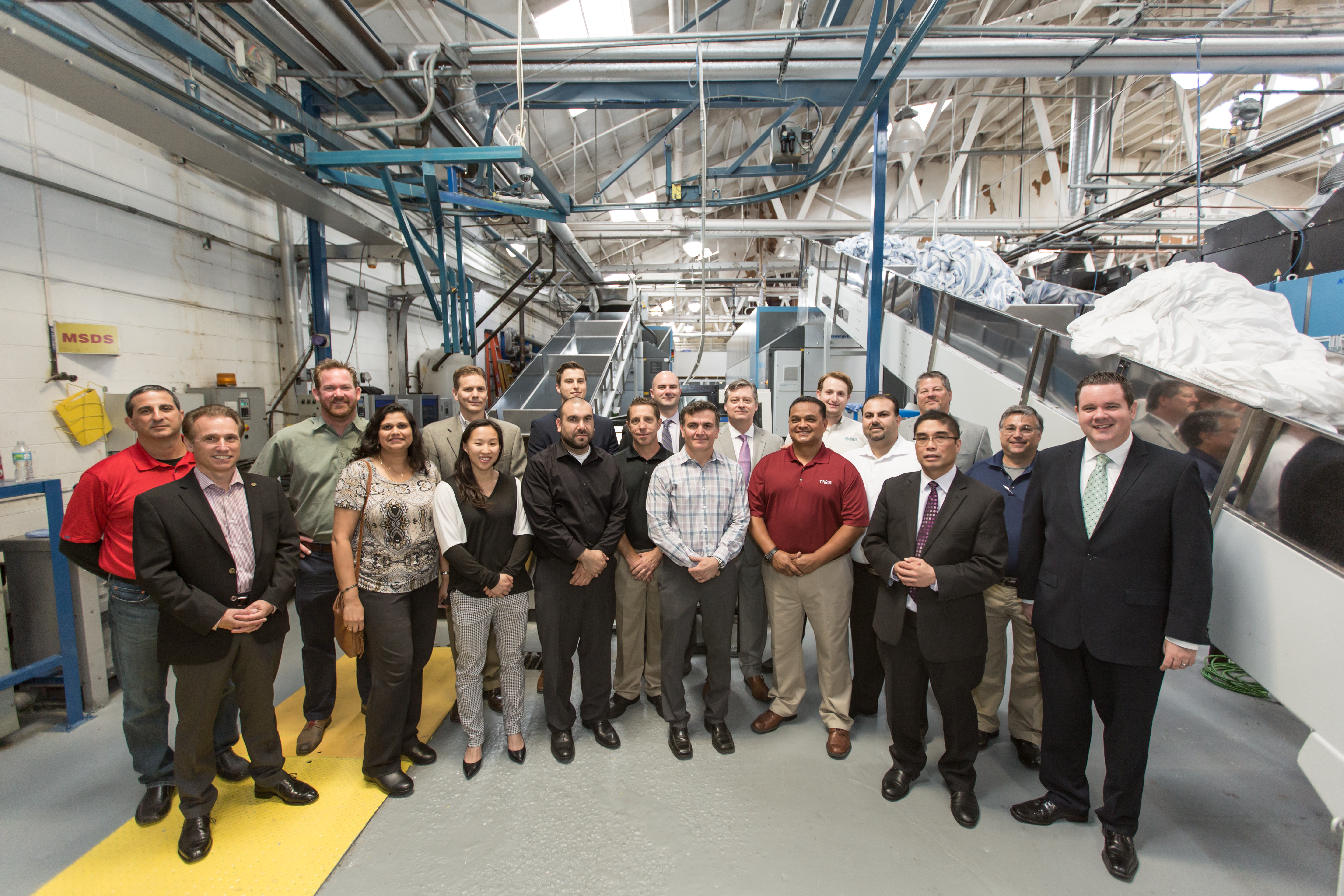
By Matt Wilson Laundry Design Specialist, Kannegiesser
Many times laundry owners/managers will delay upgrades to their facility due to concerns of cost or what they perceive to be an inconvenience to their customers via disruptions in the laundry process from equipment replacement or building expansion. Or maybe there’s just too much on their to-do list, and having to consider what the needs and future needs of their laundry will be, in addition to how they can meet those needs, keeps falling to the bottom of the list.
When working with a reputable laundry design specialist, all of the above considerations can easily be overcome, and moving forward with a laundry upgrade can prove to be very beneficial to both a laundry – and its customers.
With advances in technology and efficiency, many laundries are improving their process, throughput and energy-saving capabilities by upgrading their laundry equipment. While the capital investment can be substantial, the benefits can be substantial, as well.
Case Study – Magic Laundry Services
Magic Laundry Services in Montebello, California, processes hospitality linens as well as providing a rental service for hotel, restaurant and in-room dining linens. Recently the facility revamped its facility with Kannegiesser equipment, investing $4 million to renovate and expand to better serve its customers. The process wasn’t easy, but the results transformed Magic Laundry Services and its business. Here’s how we did it, choosing the right mix of equipment and making major renovations around Magic’s busy schedule.
The process of updating Magic Laundry Services began with extensive conversations with the Kannegiesser design and engineering teams, who created CAD drawings of equipment layouts that would maximize space and achieve the facility’s production goals. On-site visits were conducted to view the space and verify that the designs were appropriate for Magic Laundry Services’ needs. Once the layout was finalized, meetings with Magic Laundry Services’ staff, its contractors and Kannegiesser’s project management team defined responsibilities and determined the installation schedule.
Maximizing Production Throughout Renovations
The Magic Laundry Services upgrade took a unique, phased approach. Scheduled around the winter holiday season, Phase 1 of the upgrade was scheduled to be completed in 14 days right before Christmas,. This phase included the removal one tunnel washer, press, and five dryers and then the installation of one 13-compartment, 132-pound batch tunnel washer, one 56-bar press extractor and four double-batch system dryers. Phase 2, which included the removal of a second tunnel, press and five dryers and replaced with second 13-compartment, 132-pound tunnel washer, 56-bar press extractor and six additional double-batch system dryers, was scheduled to be installed immediately after New Year’s Day.
With the clock ticking, the Magic Laundry Services, Kannegiesser and construction teams needed a solid plan and good communication to get the job done. Kannegiesser provided four technicians and a project manager on-site to ensure that the upgrade process proceeded smoothly with the least amount of disruption to the laundry.
Each phase of installation went smoothly, and by the end of January, both tunnel washing systems were operating at full capacity, thanks to the teams’ dedicated efforts. The results of this hard work are visible throughout Magic Laundry Services.
Increased Capacity & Efficiency – Decreased Environmental Footprint
With a tunnel system that can now wash a combined 7,200 pounds per hour, the throughput of the facility has increased by 30%.. Magic Laundry Services also transformed its energy efficiency capabilities with water reuse tanks and ratio metric washing Water and chemicals for cleaning are completely customized by batch weight, meaning that these items are conserved by the tunnel. This has led to 8% reduction in water usage even with the increased throughput. They also were able to decrease their gas usage by 15% with the new more efficient Kannegiesser dryers with the Eco2Power option. Also they are now saving 10-12% on electricity with the new system. These efficiency gains have even resulted in an energy credit from Magic Laundry Services’ utility provider. In the competitive and eco-friendly market of Southern California, efficiency tends to draw new customers.
Thanks to its system upgrade, Magic Laundry Services has made vast improvements in its laundry capabilities. With help from the Kannegiesser design and installation team, the facility now has equipment that is perfectly suited to its space and needs, and has made energy efficiency gains that will also result in valuable cost savings for the company. With a full-service approach to its upgrade, Magic Laundry Services is set up for future success.
About the Author
Matt Wilson, Laundry Design Specialist, Kannegiesser
Matt Wilson is a designer and project manager working with a team of two other project managers, another designer and twenty one technicians. The Kannegiesser team has completed fifty eight installations in the past year.
For more information, visit the company’s web site: Kannegiesser