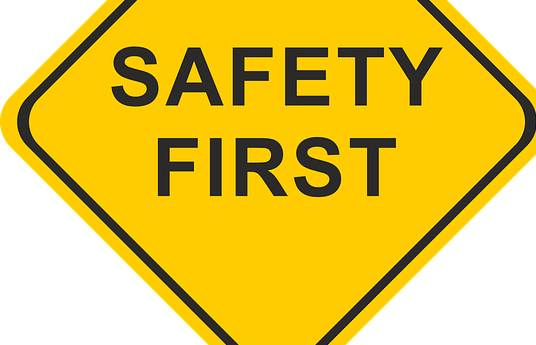
Four linen and uniform service industry TRSA members and two associates (suppliers to the industry) are 2020 SafeTRSA Excellence Award winners, honored for their projects or achievements that produced or reflected safety gains due to support from top management, employee involvement, training or good communication.
Associate winners:
Rotomolded cart manufacturer Meese, Ashtabula, Ohio, having identified hazards in its molding process, used the “hierarchy of controls” [assessing best opportunities for hazard protection from PPE (least protective) to hazard elimination (most)] to redesign molding workstations. The new units dramatically reduce the risk of slips, trips and falls related to working from a small, elevated, open platform. Stair and platform redesign also decreased ergonomic hazards and fatigue. Platforms were widened and made with adjustable legs to accommodate different sized workers. Railings and safety gates were added to the platforms and wood was used for floors and stairs instead of steel. Bins for tools, parts and resin powder and trash receptacles became integral to the stations, eliminating the need to step off the platform to retrieve these.
The Ecolab Textile Care division’s role in the company’s Goal Zero program protects employees and laundry customers. Its bulk verification process for digitally verifying the correct product is delivered to the right customer in the right tank also protects the environment. The St. Paul, Minn.-based division uses Intelex, a global web-based system for compliance and management functions to foresee safety concerns and eliminate risks before they lead to accidents. A safety course each year and behind-the wheel training every three years is given to drivers. CarChip, Virtual Risk Manager (VRM) and Mentor applications guide behavior changes and prevent incidents. In chemical production, a global lockout/tagout policy reduces injury risk; technicians working in laundries benefit from an electrical safety training program that guides repair of chemical dispensers.
Linen and uniform service winners:
Barely 18 months in existence, Cooperative Laundry, a Kearny, N.J. hospitality laundry start-up, is building a safety culture that encompasses all employees and focuses most tightly on engineers. Safety is viewed as the foundation and pinnacle of the business, with these pillars (principles) upholding the goal of zero unsafe acts, failures and surprises: ownership (safety is everyone’s job), questioning attitude (to discover unsafe situations), knowledge, communication and teamwork. Lost time has been 1 percent of total hours; 1.5 percent including temporary accommodations or job placement. Leading the way in minimizing risk: training workers to push carts instead of pulling them. Engineers have had just two reportable incidents, prompting their better adherence to standard operating procedures and retraining in machine guarding.
NOVO Health Services, the Atlanta-based operator of four healthcare linen service laundries, demonstrates safety excellence through management leadership, employee involvement, worksite analysis, hazard prevention and control, and safety and health training. The company’s Safety and Health Manual includes 25 comprehensive policies for which specific training has been developed and presented as appropriate. An online program assigns monthly tasks with required completion dates, including training, fire drills, emergency action plan review, OSHA-required record review and submission, and local- and corporate-team audits specifying corrective action. From 2017 to 2019, Novo’s total recordable injury and illness rate (TRIR) is 3.4 and days away from work, reassignment or transfer (DART) rate is 2.0; in 2019 alone, 3.0 and 1.7. Industrywide these figures are 5.2 and 3.5.
A 100-year provider of industrial and retail medical linens and a member of the Healthcare Linen Services Group, Logan’s Uniform, Shelbyville, Ky., has a long history of little or no safety issues. It had no recordable incidents in 2019 and hasn’t had a lost-time incident since January 2017. The company attributes this success in part to a “culture of care” supported by years of safety expertise and daily monitoring. Employee behavior is vigilantly observed and corrected as needed. When an individual performs any hazardous task, a colleague or manager is present for its duration. Incentives or bonuses are provided for no incidence. Sales and service personnel hear about safety on a regular basis, with discussion of proper lifting and loading techniques and hazards of driving and servicing customers.
UniFirst Corp.’s Partners in Safety program awards points to employees each quarter based on their safety metrics and on-the-spot for getting “caught being safe.” This international uniform service chain’s program encourages employees to set safety goals and rewards them when these goals are met. A website dedicated to the program provides points-awarding engagement opportunities and enables employees to redeem points for their choice of thousands of items. The longer an employee works safely, the more points accumulated and the more valuable items that can be redeemed. The program launched throughout the Wilmington, Mass.-based chain in second quarter 2018; by year’s end, 897 incentive orders were received; a year later, 1,692. Same time, worker’s compensation claims fell 13 percent; TRIR, 14 percent; and DART, 11 percent.