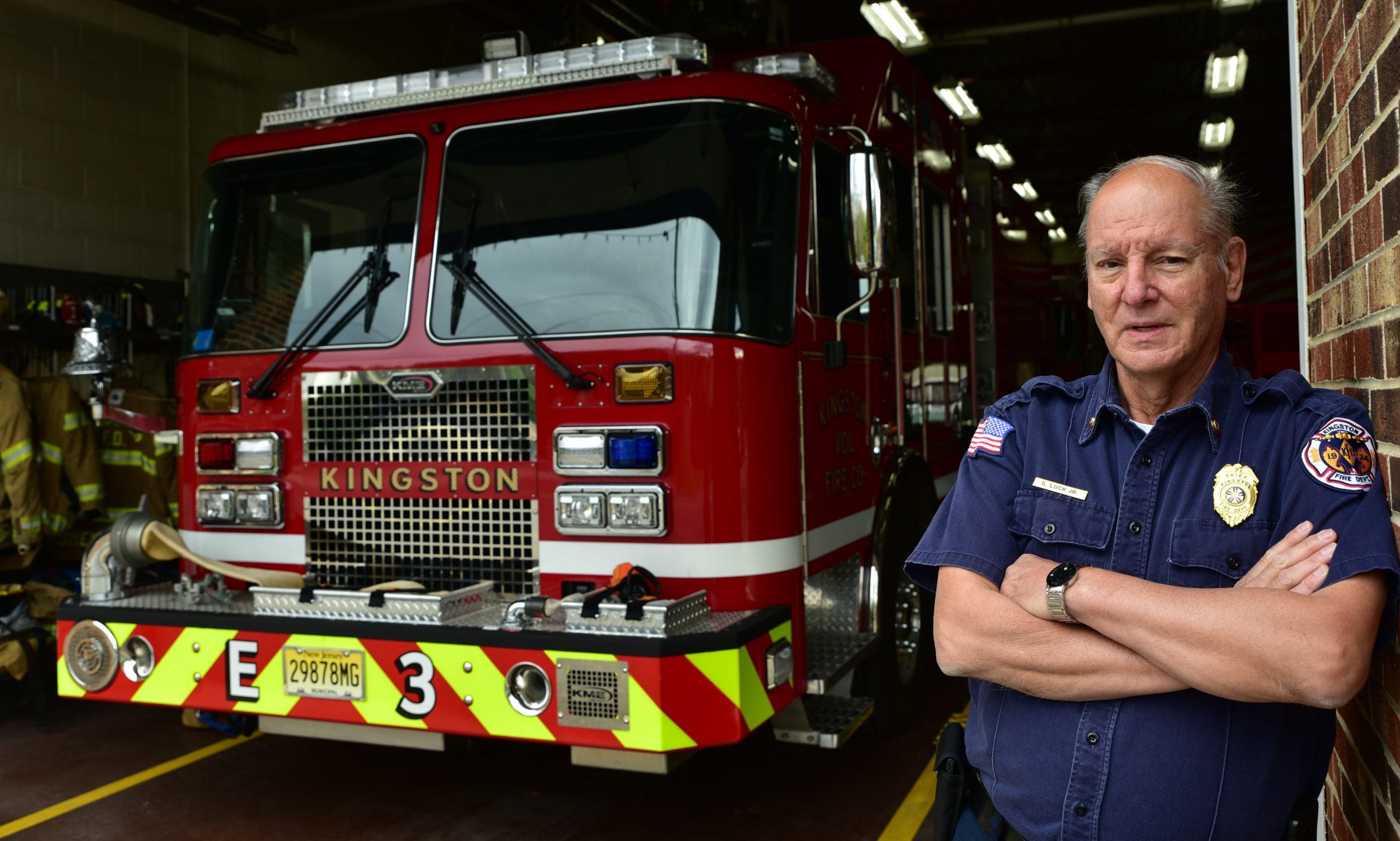
Changing times have been challenging PPE and safety needs for fire departments and evolving National Fire Protection Association (NFPA) standards for decontamination of gear are top concerns. No one knows that more than Chief George Luck, Jr. at New Jersey’s Kingston Volunteer Fire Department. The 96-year-old department has always adapted with the times to serve its community.
A small town in central New Jersey, Kingston is a sleepy commuter suburb with buildings that range from historic homes dating back to the Revolutionary War, to modern corporations, hotels, assisted living facilities and North American headquarters for global pharmaceutical giants. The constant, for the past nearly 100 years, has been the dedication and commitment of the Kingston Fire Department.
The needs of this small, mighty force have evolved. Updating their station equipment to address critical decontamination imperatives of today’s firefighting environment has been a big priority for Chief Luck and the District’s board of commissioners. For years, Kingston firefighters sent their turnout gear out to a neighboring department to have it cleaned and decontaminated. This left the Kingston team and its community vulnerable when gear was out for cleaning. With the support of the District’s Board of Commissioners, Chief Luck justified that it was time to invest in onsite decontamination and cleaning equipment for the station to reduce his crew’s exposure to toxic contaminants.
After a competitive bid process, Chief Luck turned to Miele, the family-owned, professional laundry technology company that has been driving innovation in laundry for 120 years to meet the unique needs of textile and fabricare like those of his volunteer fire crew.
“As a relatively small volunteer fire department, our firefighters often can’t afford to have multiple sets of gear,” said Luck. “The Miele system enables our crew to wash their gear immediately after we get back to the station from a call and return it to service within a few hours. That turnaround time matters when seconds count.”Miele’s John Lubas, professional technical manager, worked closely with Chief Luck to develop an on-site solution that would solve Kingston’s need for quick-turn, effective decontamination and reprocessing of FR (flame resistant) gear while preserving vapor barrier attributes of the equipment. Additionally, Kingston needed to ensure the solution would deliver rapid drying capabilities and could fit into limited, existing space at the station.
“Our firefighters are volunteers who aren’t here every day to use the equipment, so we needed something that could be easily programmed and still completely disinfect and re-process not only our turnout gear, but also can clean our gloves, face masks, station wear uniforms, rags from washing the trucks and more,” Luck said. “It’s also important to us as a small district to ensure we don’t pollute our waterways, so the limited environmental impact and reduced water use of the Miele system was a big consideration as well.”
With limited resources, the Kingston station was particularly focused on ensuring that their gear remains in good shape, and that means preserving the integrity of specialty FR and vapor barrier textiles to remain compliant with NFPA standards.
The Miele team installed its 25-pound capacity Performance Plus PW 811 washer and PT 8303 dryer system in spring 2020. Miele’s Performance Plus PW811 is user-friendly, easy to install boasts the technology to reduce infection potential and minimize utility costs. It works as a system with Miele’s PT 8303 dryer that alternates tumbling action for improved garment dispersion and to ensure consistent and even, crease-free drying.
Additionally, Lubas brought in partner and textile cleaning specialists Kreussler. Miele and Kreussler’s collaboration has enabled both companies to maximize their R&D efforts to respond to the rapidly evolving PPE textile.
“The first rule of PPE is do no harm, meaning the chemistry of cleaning solutions has to address the inherent safety features of the material,” says Rich Fitzpatrick, vice president, Kreussler. “In turnout gear, each layer has highly specific temperature thresholds, chemical protectants, reflective attributes, breathability or other sensitive and specific attributes, so the chemistry and the equipment have to work together to disinfect, remove grease and stains and toxic contaminants — without affecting each fabric’s ability to do its job.”
The right chemistry is extremely important, and one of several variables that factor into ensuring turnout gear is properly decontaminated and ready to be put back into service. The right program, highly tuned mechanical action, specific chemistry, load size and time all contribute to the end result and ultimate effectiveness and safety of firefighters’ lifesaving PPE.
“Firefighters and first responders put their lives on the line to protect us every day,” says Paulo Rocha, Miele’s Head of Commercial Laundry, Dishwashing and Marine. “When that siren goes off, they do not have time to wonder if their gear is going to protect them, or worse yet, harm them. I’m proud of the fact that I can say with confidence that Miele technology delivers vital protection to them in return.”
“We take safety very seriously, and our people are our greatest asset,” Chief Luck says. “Some of our members are 4th and 5th generation volunteer firefighters with our department and have served for decades. Our members are part of this community too, so it’s important that we invest in the best equipment that will help keep them safe. For us, that is Miele.”