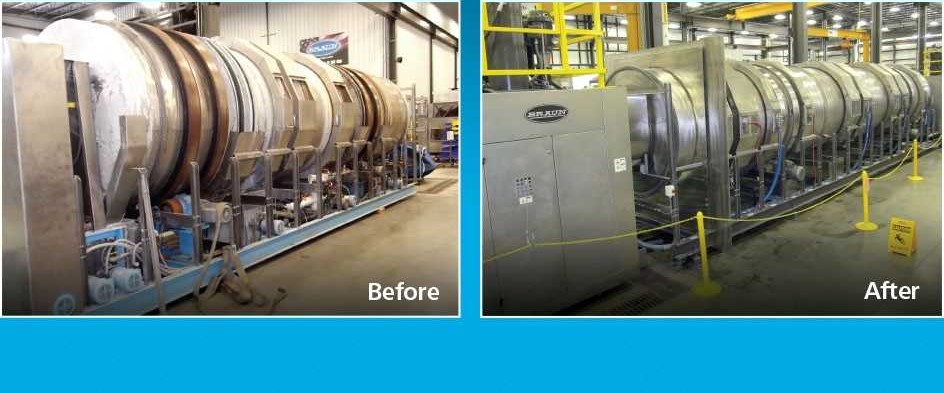
By Joe Gudenburr, President, GA Braun
Editor Note: In Part One of Embracing Green at Braun…An Operational Way of Life, the need to embrace change and a green way of life was discussed. Today we’ll look at the specific green initiatives instituted at the Braun Manufacturing facility which the company is embracing as an operational way of life. Photo top right: Braun’s Certified Remanufactured Equipment.
In the Braun manufacturing facility we have made a host of changes to operating practices, and we have also spent a good deal of capital to improve our overall efficiency. On the practices side we have institutionalized the 100% recycling of all wood, steel, and card board utilized in our daily operations. This means all materials received by us or used in the generation of our end products that fall into these categories that used to go the dumpster and hence the landfill or incinerator are recycled. This initiative was put into place in the early 2000’s and today we recycle an average of 1,560 cubic yards of paper and cardboard out of our factory. At this same time, we went from having pallets incinerated to recycling them into mulch through a partnership with a local manufacturer.
Obviously, as a heavy equipment manufacturer we use a significant amount of steel. Through our capital investment in highly automated equipment and strategic utilization planning of the material we process we have been able to virtually eliminate scrap material. What little waste we do produce whether it be aluminum, carbon steel, stainless steel, copper or brass is recycled through our local recycling centers.
In the last 10 years we have made significant investments in energy efficient infrastructure in the form of a new plant, extensive plant expansion, the installation of high efficiency boilers and compressors, and LED lighting (it should be noted that when we eliminated all of our original T5 lighting which was the most efficient at the time the initial factory was built, that we repurposed these fixtures with local manufacturers to replace their older technology). All were strategic investments that we were able to leverage grant funds to support, and anyone reading this article should get educated on what grants and incentives may be available to you via your local, State governments. In 2006 we converted a good deal of our painting operations over to powder coating, and at the same time altered our wet painting process. The combined benefit of this change has been a reduction of VOC emissions in the neighborhood of 6 tons per year. The most recent decision we made was to leverage hydropower for roughly ½ of our electricity needs. Although this is not necessarily a cheaper solution it is a clean and green alternative to fossil fuels as the hydro plants do not emit greenhouse gases and other pollutants.
As if all of these plant efforts aren’t exciting enough the real exciting development over the last 5 years has been our remanufacturing process. In the last three years alone, we have remanufactured numerous machines preventing over 605 TONS of steel from going either to the scrap yard or recycling center. Why is this so significant? This means that we reduced the need to produce this material at the mills, and that we have had a significant impact on the environment through the many savings that this represents. This means that we have been able to bring machines back to life after 20+ years of dedicated service and return them to the market rebuilt to current day specifications with a new equipment warranty. This not only is great for the environment, but it presents a significant savings opportunity for our client partners. The only negative is that not all products are logical candidates for remanufacturing as certain machines which do not contain a large steel content simply don’t afford the economics to support the costs to return said machines to new.
As we dug deeper into the remanufacturing process we found that we could invest capital in a green sandblasting operation which afforded us a more efficient and clean solution for preparing machines for this process. Concurrently, we found that we could recover or repurpose many of the components (electrical, pneumatic, mechanical, and hydraulic) that were removed from the old machines as they were disassembled. The outcome of this effort is an offering we now call our “R-part” program. By handling components with care, applying a detailed inspection and testing protocol (in some cases having the components repaired) we were able to create a dedicated inventory of lower cost parts alternative for our client partners. We have motors, cylinders, baskets, control boards, inverters, etc. that are available depending on our current inventory. We have found that many of our clients truly appreciate this as they are looking for older components that may be challenging to find, or expensive given the need that they have. Also, as a client has a machine that may be within the last few years of use they don’t want to spend the long dollar on new parts only to not exhaust the life of said components. As a result, these clients will often opt for the lower cost R-part as it meets their needs. Again, this effort has kept dumpsters loads of components from going to the scrap yard before their time and provided a way to lower the cost of operations for our client partners……win / win!!!
At the end of the day it is amazing to see how best practices, and a continuous improvement mindset have aligned with being green. This journey does require work, dedication, and discipline. However, the rewards are significant not only for all who are impacted by the outcomes of these efforts.
For more information, visit the company’s web site: GA Braun